Surfactants
Toluene diisocyanate (TDI) is a crucial aromatic diisocyanate widely used in the production of polyurethane foams, coatings, adhesives, and sealants. As a key isocyanate component, TDI reacts with polyols to form versatile polyurethane materials.
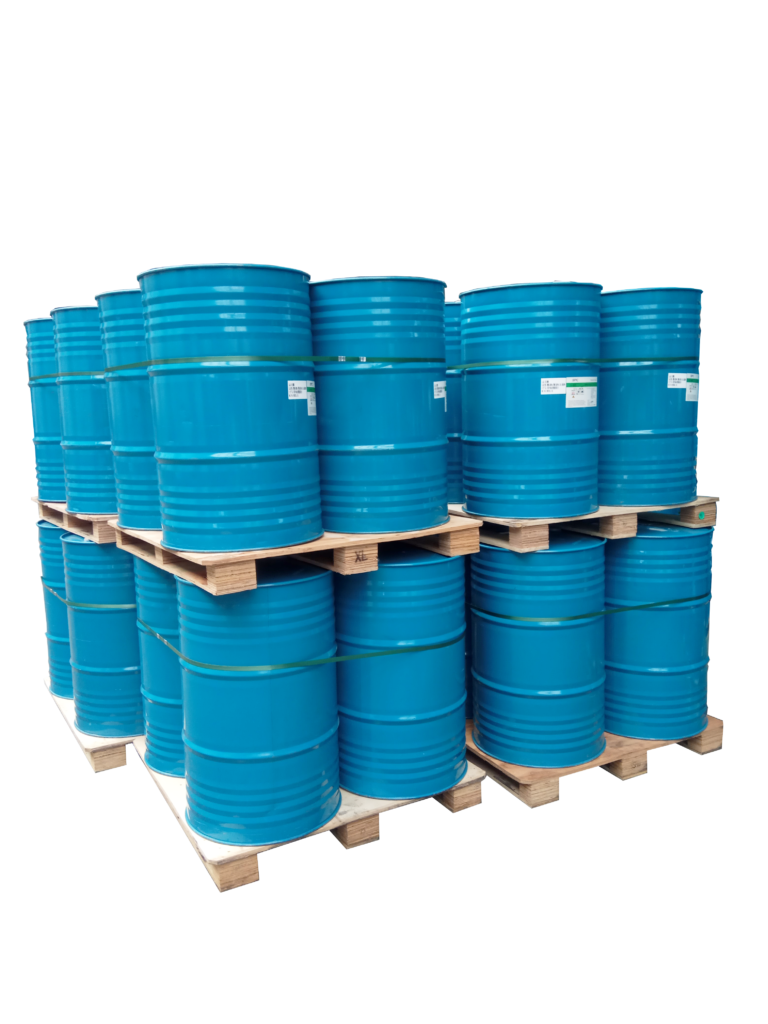
Toluene Diisocyanate
Toluene diisocyanate (TDI) is a pivotal aromatic diisocyanate extensively utilized in the polyurethane industry. Its primary roles include:
Chemical Reactivity: TDI exhibits high chemical reactivity, enabling it to readily react with compounds containing active hydrogen atoms, such as water, alcohols, and amines, to form corresponding polymers.
Applications:
- Flexible Polyurethane Foams: TDI is predominantly used in the production of flexible polyurethane foams, which are integral components in furniture, bedding, and automotive seating.
- Elastomers: TDI contributes to the synthesis of polyurethane elastomers, providing materials with exceptional elasticity and abrasion resistance.
- Coatings and Adhesives: TDI is employed in the formulation of polyurethane-based coatings and adhesives, offering superior adhesion and durability.
In summary, TDI serves as a crucial isocyanate component in polyurethane synthesis, with its selection and application directly influencing the performance characteristics and applicability of polyurethane products.
Why Choose Us
Types of Toluene Diisocyanate
Description | Application |
Mixture of 98% 2,4-Toluene Diisocyanate. | It is mainly used in the cast elastomers and the paint/coatings industries. |
Mixture of 80% 2,4-Toluene Diisocyanate and 20% 2,6-Toluene Diisocyanate | It is mainly used in the preparation of flexible polyurethane foam and non-foam urethanes. |
Mixture of 65% 2,4-Toluene Diisocyanate and 35% 2,7-Toluene Diisocyanate. | It is mainly used tin the preparation of high-resilience flexible foams. |

Common types of surfactants used in PU
In the polyurethane production process, surfactants play a key role and are mainly used to regulate the formation and stability of foam. Common types of surfactants include:
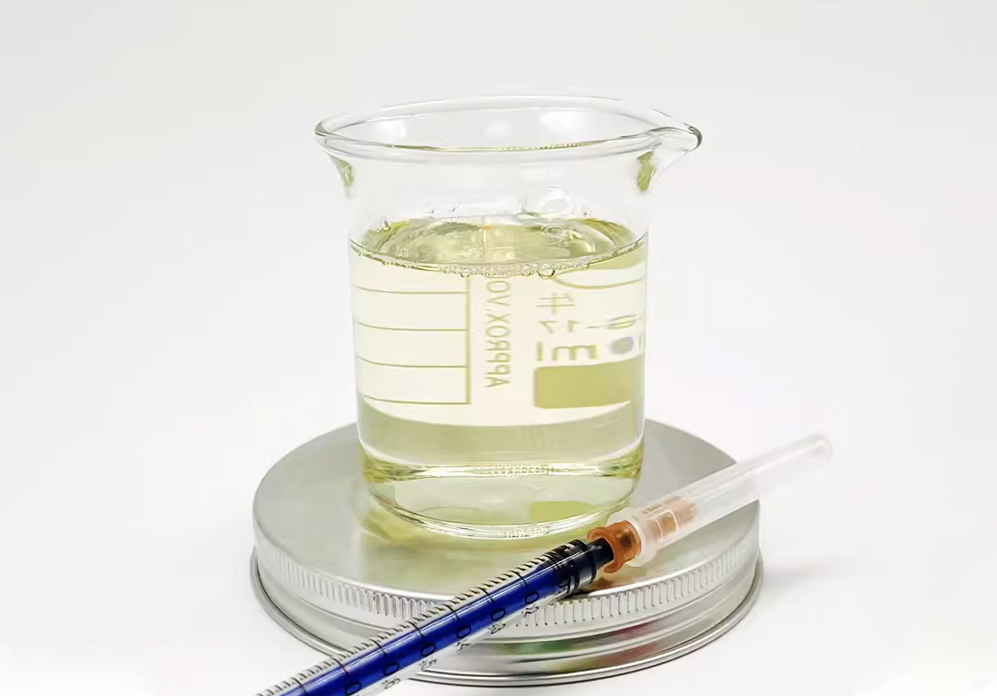
Amphoteric surfactants:
· Function: Depending on the acidity and alkalinity of the solution, these surfactants can be anionic or cationic, with good compatibility and mild properties, and are often used in polyurethane products that require special properties.
· Cocamidopropyl betaine (CAPB): This is a common amphoteric surfactant with mild properties and is widely used in personal care products, but its application in the polyurethane industry is relatively rare.
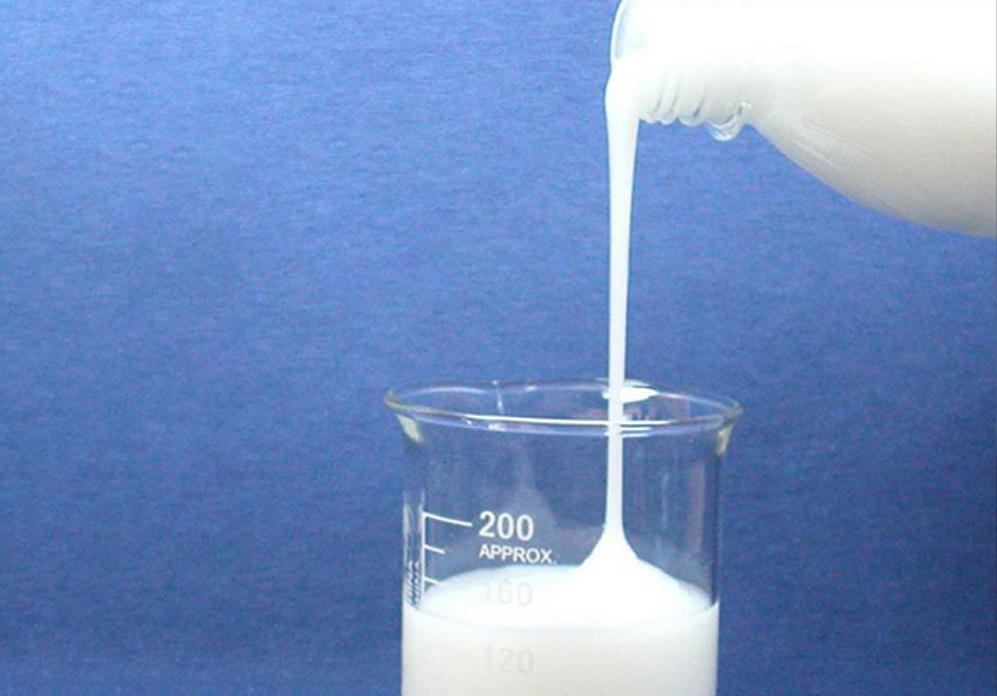
Polyether surfactants:
· Function:It has good emulsification and dispersibility, helps to form a uniform foam structure, and improves the physical properties of the foam.
· Polyoxyethylene-polyoxypropylene block copolymer (Pluronic series): This type of non-ionic surfactant is composed of ethylene oxide and propylene oxide units, has good emulsification and wetting properties, and is suitable for a variety of polyurethane systems.
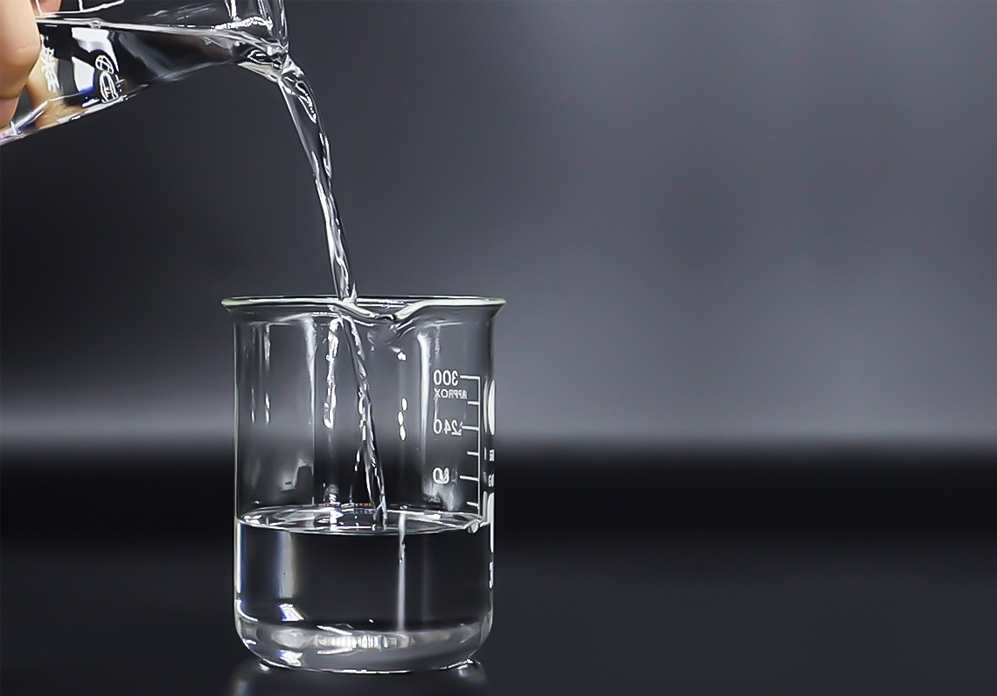
Silicone surfactants:
· Function: By reducing surface tension, improving the uniformity and stability of foam, it is widely used in the production of soft and hard polyurethane foam.
· Polydimethylsiloxane (PDMS): This is a linear silicone polymer with excellent surface activity and thermal stability, and is often used to regulate the fineness and stability of foam.
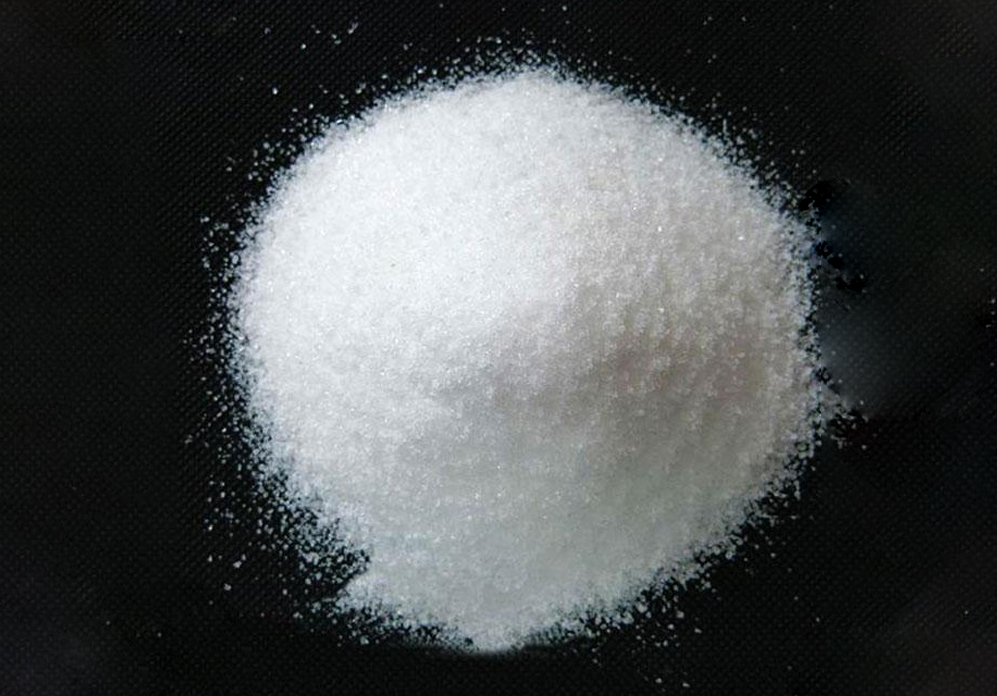
Anionic surfactants:
· Function: Dissociate negatively charged hydrophilic groups in aqueous solution, commonly used in polyurethane systems that need to enhance wettability and dispersibility.
· Sodium dodecyl sulfate (SDS): This is a common anionic surfactant with good detergency and foaming ability, but it is rarely used in polyurethane foam production.

Cationic surfactants:
· Function: Dissociate positively charged hydrophilic groups in aqueous solution, suitable for specific polyurethane application scenarios, providing antistatic and sterilization functions.
· Cetyltrimethylammonium bromide (CTAB): This cationic surfactant is mainly used in specific industrial applications and has limited application in polyurethane foam production.
Selecting the right surfactant type and composition is crucial to controlling the quality and performance of polyurethane foam. In practical applications, the most suitable surfactant should be selected according to the specific production process and product requirements to achieve the best foam performance.
Clients Love
Testimonial
The quality and performance of these polyurethane products are exceptional, perfectly aligning with our industrial requirements.